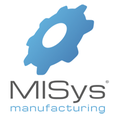
MISys Manufacturing
Basic Manufacturing
Like other inventory systems, MISys can tell you what you have in stock and where its located. For MISys Manufacturing customers, that's simply not enough. Our customers enjoy a typical savings of 25% in inventory carrying costs because MISys has the ability to order only what you need, when you need it. Every manufacturer needs the functionality included in the Basic Manufacturing module of MISys Manufacturing. Inventory control of raw materials and WIP, multi-level bills of material, BOM revision control, physical inventory cycle counting, and production work order processing. Start with one user license and expand with up to 256 concurrent users.
WHAT'S IN BASIC MANUFACTURING
- Manufacturing Inventory – Raw Materials and WIP
- Item Master Files
- Supplier Information
- Bills of Material, 16 Levels Deep
- Multiple Warehouse Locations
- Work Orders
- Production Schedule
FUNCTIONALITY
- Use MISys to track raw materials and Work In Process (WIP).
- Create, maintain and revise multi-level Bills of Material (BOM) with full explosion to 16 levels.
- Maintain physical inventory on a net-change basis using cycle counting, eliminating the agony of annual inventory counts.
- Utilize standard, average, LIFO or FIFO costing methods that match your accounting practices.
- Generate Work Orders to document and track production activity.
- Create personalized alerts to warn of critical events and status in your operation.
- Track inventory in multiple warehouse locations. Move inventory from one location to any other.
- Maintain inventory levels with minimum, maximum and reorder points.
- Instantly display transaction history, where items are used (BOM Implosion) and outstanding order status.
- ...and more.
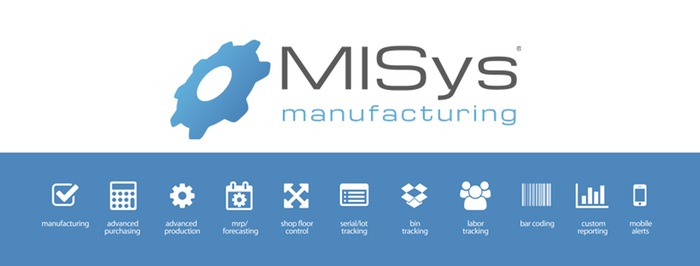
Advanced Purchasing
If you need purchasing capabilities uniquely suited to a manufacturing firm, consider licensing the optional Advanced Purchasing module. With just a few clicks, you'll be able to analyze your material shortages and automatically create all of the purchase orders needed to replenish your inventory.
WHAT'S IN ADVANCED PURCHASING?
- Purchase Orders
- Integration with A/P in the accounting system
- Supplier details
- Supplier pricing levels
- Detailed costing analysis
FUNCTIONALITY
- Expedite or close orders at any time with any quantity received.
- Transfer invoicing data directly to Bills in Accounts.
- Expedite purchase order by dragging end date on easy to use Gantt chart display of purchase orders over time.
- ...and more.
- Create, print, email and track formal purchase orders.
- Automatically detect quantity-based price breaks for each item and qualified supplier, and revise purchase orders.
- Calculate tax due for taxable items by supplier.
- Instantly update raw materials inventory from purchase order receipts.
- Define and apply additional cost for accurate landed cost tracking.
- Expedite purchase orders to assist in production scheduling.
- Print internal purchase order approvals and multi-page purchase orders.
- Specify purchase order formats to fit virtually any preprinted form or print on plain paper.
- Email purchase orders with user-defined body text and automatically attached PDF file of the order.
- Place blanket orders with scheduled delivery dates.
- Copy previous orders to speed up order generation.
- Receive items individually or by exception.
- Print optional purchase order receiver.
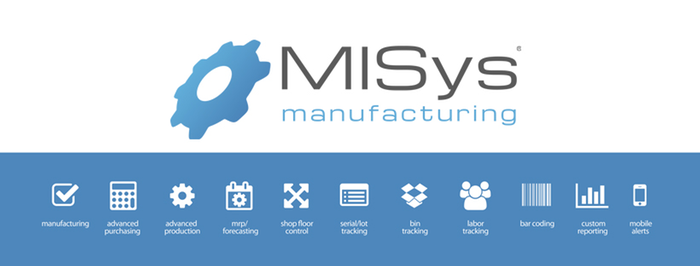
Advanced Production
Job shops and manufacturers who create variants of standard assemblies (or custom orders for special "one-off" items) will discover that the Advanced Production module provides them with critical importation needed to track their production activities. With Advanced Production, you'll be able to predict the cost of every job and track your performance.
WHAT'S IN ADVANCED PRODUCTION?
- Manufacturing Orders (MO's)
- Customized Job Orders
- Cost Estimating and Tracking
FUNCTIONALITY
- Use Bills of Material with Routing Details through Work Centers to guide shop floor operations.
- Create and print cost estimates based on the unit cost of known components and the estimated cost of provisional items.
- Compare projected manufacturing cost with the actual cost for accurate analyses of productivity and profitability.
- Declare provisional items that may not be completely defined, or are unknown at the time.
- Associate jobs with manufacturing orders for detailed cost analysis.
- Edit manufacturing orders to create custom job orders.
- Allocate special items such as labor, supplies, and tooling to customize manufacturing order.
- Attach files and pictures to MO's to provide unlimited amounts of online documentation.
- Create and link child MO's to any parent MO.
- Copy previous orders to speed up order generation.
- Print internal manufacturing order approvals and multi-page production manufacturing orders.
- Create and print job travelers to accompany jobs on the shop floor.
- Analyze standard, projected, and actual job costs with performance variances.
- Create detailed manufacturing order pick lists.
- ...and more.
- Create Manufacturing Orders either from a standard bill of materials, or from scratch without previously defined components.

Material Requirements Planning
If you need to plan your production and purchasing activities weeks, months, even years in advance, you'll want to license the Material Requirements Planning (MRP) module. With just a few mouse-clicks, you can create a detailed Master Production Schedule which analyzes your current inventory in the context of open purchase orders, work orders, manufacturing orders, and (optionally) sales orders. Spot impending shortages while there is still time to respond. Click again to create all the required purchase orders and production orders. MRP has never been easier.
WHAT'S IN MATERIAL REQUIREMENTS PLANNING?
- Master Production Scheduling (MPS)
- Sales Forecasting
- Material Requirements Planning
FUNCTIONALITY
- Manually or automatically create purchase orders and production orders based on the MRP.
- Save and re-open multiple production schedules.
- Share production schedules among workgroup users.
- Include or ignore current inventory, purchase orders, and production orders in the MPS.
- Create and maintain batches of scheduling events.
- Fix production start dates and schedule forward to completion.
- Create a Master Production Schedule (MPS) for net of current stock, purchase orders, production orders, and sales orders.
- Maintain a work calendar that accounts for full production days of the plant as well as partial or non-production days.
- Define an MPS for any locations and range of dates.
- Create a Material Requirements Plan based on any selected MPS.
- Manually schedule order releases to resolve shortages.
- Automatically schedule Just In Time (JIT) order releases to resolve shortages.
- Maintain and apply sales forecasts to future production schedules.
- Perform simulations to analyze the effect of future production scenarios.
- ...and more.
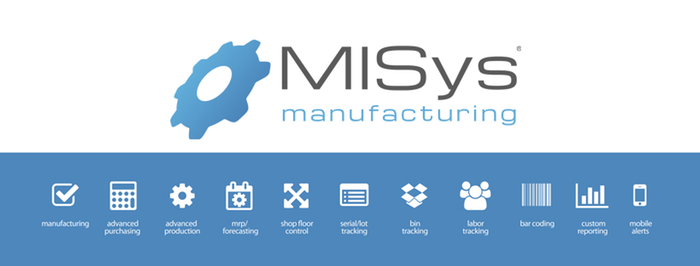
Shop Floor Control
Clear definition of each production operation is the key to effective manufacturing business management. Shop Floor Control delivers the ultimate solution to running a manufacturing plant profitably by allowing you to accurately predict production costs based on estimated material, labor, and overhead, and allowing you to analyze actual production costs.
WHAT'S IN SHOP FLOOR CONTROL?
- Tool Management
- Work Center Management
- Shop Operations Management
- Capacity Management
FUNCTIONALITY
- Track the use and maintenance of production tools.
- Be alerted whenever tools require maintenance or replacement.
- Establish work centers for all production activities.
- Define rates at which each work center can process its work.
- Define days of the week when each work center is open.
- Define an unlimited number of splits per shift, including optional splits for overtime, reserve labor, etc.
- Define required material, labor, and overhead for each work center.
- Roll up material, labor, and overhead costs throughout the entire product structure.
- Create routing details for bills of material and manufacturing orders.
- Estimate assembly times for any production quantity.
- Predict start date for given completion date.
- Predict completion date for given start date.
- Accurately estimate manufacturing costs based on combined material, labor, and overhead.
- Post shop operations to individual production operations.
- Compare actual to estimated manufacturing costs with detailed variance reports.
- Adjust routings to reflect the actual time required to perform an operation.
- Analyze production efficiency for each manufacturing order operation.
- View work center loading for any range of dates.
- ...and more.
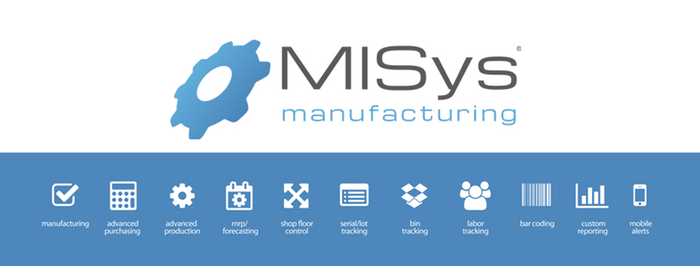
Serial/Lot Tracking
Manufacturers needing to track serial or lot numbers, not just for finished goods but throughout the entire purchasing and production process, will find that the optional Serial/Lot Tracking module allows them to comply with strict regulatory agency requirements, including FDA and FAA.
IDEAL FOR MANUFACTURERS OF:
- Automotive
- Food Products
- Medical Devices
- Pharmaceuticals
- Defense and Aerospace
SATISIFIES THE REGULATORY REQUIREMENTS OF:
- US Food and Drug Administration
- US Federal Aviation Administration
- ISO 9000
FUNCTIONALITY
- Set up the system to be able to track by item, serial number or lot number.
- Establish and assign sequential serial and lot numbers.
- Adjust numbers that have been previously assigned.
- Generate reports by stock status, history, where used, component lists, manufacturing orders.
- Transfer serial numbers to finished goods in accounting software (where available).
- Transfer serial numbers to a sales order in accounting software (where available).
- Transfer lot numbers to finished goods in accounting software (where available).
- Identify the assembly, subassembly or MO in which the tracked item was used.
- Identify the quantities of a serial/lot tracked remaining in stock.
- ...and more.
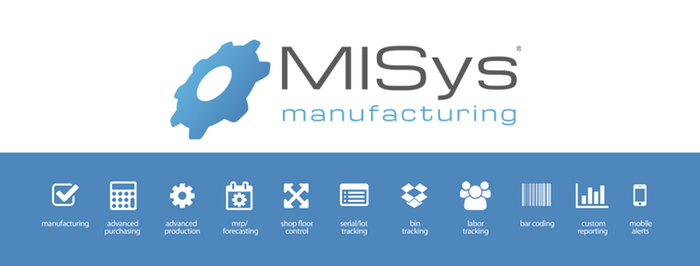
Bin Tracking
If your business requires that you keep your raw materials, sub-assemblies, or finished goods inventory in specific containers (bins, bales, bolts, etc.), the optional Bin Tracking module allows you to maintain a unique inventory sub-location for every item or assembly.
FUNCTIONALITY
- Keep raw materials, sub-assemblies or finished goods inventory in specific containers (Bins).
- Assign specific Bin locations for items.
- Pre-Assign Bin locations or use the Deferred or Automatic Bin Assignment modes.
- Record all bin-related transactions in the MISys Master Transaction Log.
- Track the quantity of inventory items in each container.
- Track bin locations through Purchase Orders, MO's and other functions within MISys.
- Print bar-coded Bin labels (the Bar Coding module is required).
- ...and more.
- NOTE: Although MISys Basic Manufacturing supports an unlimited number of warehouse locations, Bin Tracking allows manufacturers to track the same inventory item at several physical locations within a common warehouse.
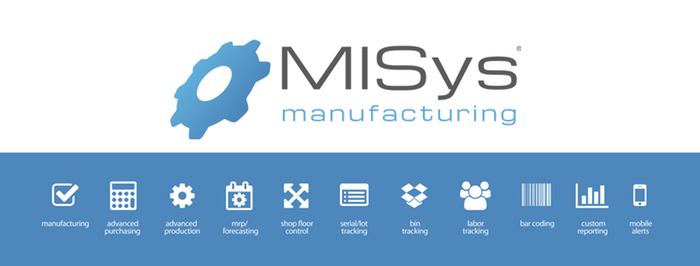
Labor Tracking
Labor Tracking keeps track of the elapsed time your production workers spend on selected Jobs and Manufacturing Orders. It automatically posts the specified quantity of any labor resourcetype Item to the Job or Manufacturing Order. Labor Tracking may be run on any PC where labor time needs to be recorded and does not require that MISys Manufacturing be installed on that computer.
FUNCTIONALITY
- Record employee activity from any PC until ready to Post to MISys Manufacturing.
- Set up Resource-type items in Item master to represent various labor rates and related overtime options.
- Charge the cost of the item (labor) to a specified Job or MO.
- Track specific employees at either a specific rate and location, or by any labor rate, or any location.
- Use the timer to record elapsed time for a specified Employee/Labor Item/Location.
- Allows for pauses and for recording comments.
- Establish alternative items (labor rates) to automatically switch to overtime rates after a specified number of timed hours.
- Operate manually as an alternative.
- Retain option of manually approving time sheet entries by switching off Auto-approve option.
- Post Time Sheet entries, two options: 1) Dispense a resource item (labor) from a Location against a specified Job, OR 2) Dispenses a resource item (labor) from the material details of the specified MO. If material details do not include the Item, it will be added automatically.
- MISys Labor Tracking communicates directly with the MISys Server module.
- There is no requirement that the MISys Client module be installed on the same computer.
- Connect once to pick up all Resource Items, Locations, Jobs and Mfg. orders for the specified MISys company database.
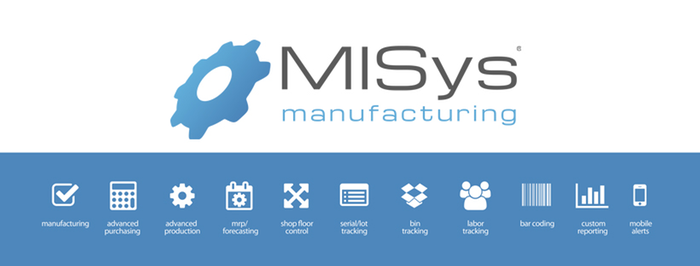
Bar Coding
MISys has developed two different bar coding systems: MISys Manufacturing Bar Coding and the enhanced MISys Worth Terminal Manager. Both systems are available with the Bar Coding module from MISys, but each requires different hardware which is sold separately.
MISys gives you two options for bar coding.
- Option 1: MISys Manufacturing Bar Coding - Developed primarily for physical inventory counts. The software works with the Worth Data T5000 bar code reader, an offline device which runs small programs on the device itself, and can collect data on the factory floor or warehouse. It must be connected to a host PC where data files can be transferred and imported into MISys Manufacturing in a batch transfer.
FUNCTIONALITY
- Update the time required for operations at various work centers.
- Conduct physical inventory by scanning bar code on shelf or item and enter quantity. - Record stock transfers as they occur.
- Record bar coded items that need to be assigned and generate new serial and lot numbers.
- Print bar coded lables on standard Avery label stock.
- Generate "Bar code enabled" reports such as Physical Inventory Worksheets, Pick Lists and Travelers to better track items used in production.
Option 2: MISys Worth Terminal Manager
- The MISys Worth Terminal Manager gives production managers and inventory managers more control from the shop floor and the warehouse. It is designed to work with Worth Data's 7000 Series RF Terminal platform connected to a Worth Data Base Station, connecting wirelessly with MISys Manufacturing. Hardware can be purchased directly from Worth Data at www.barcodehq.com.
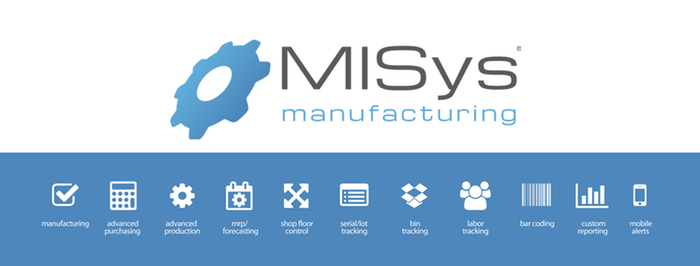
Custom Reporting
MISys STANDARD REPORTS - Make modifications to any standard MISys Manufacturing report utilizing SAP's Crystal Reports v11 or later.
- Utilize SAP's Crystal Reports v11 or later.
- Format columns according to your preferences (items, numeric formats).
- Add data from computed tables or columns.
- Add data from custom fields.
MISys QUERY REPORTS, NEW IN MISys MANUFACTURING V6.0
- Access calculated and custom fields in MISys Manufacturing data as well as many business process functions (e.g. exploded BOM views).
- *One MISys Query Designer license is included in the MISys Custom Report Module. Additional MISys Query Designer licenses can be purchased for a small charge.
- Use a set of wizards in the MISys Query Designer to create new custom reports from the information available on many MISys Manufacturing notebooks ( the Application View).
- Create a quick report using an external reporting tool that is installed by MISys Manufacturing but operates independently.
MISys ODBC REPORTS
- Create custom reports by accessing the MISys Manufacturing database using SAP's Crystal Reports and the Microsoft ODBC interface.
- Does not support custom fields, calculated data or any special business logic processing.
- Utilize MISys Manufacturing's report parameters UI widgets including finders.
- *Requires advanced knowledge of Crystal Reports and comfort with database calls.
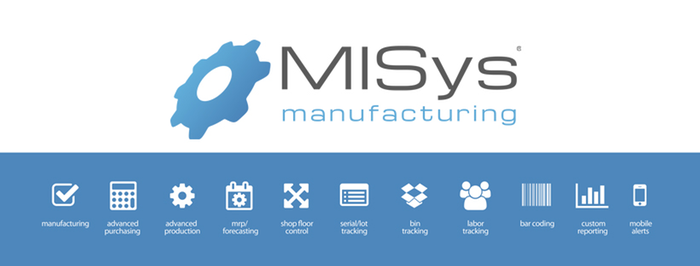
Mobile Alerts
The Mobile Alerts module allows MISys to send critical alerts to smart phones or any mobile device capable of receiving wireless email messages. The MISys Dashboard has been enhanced so that you can schedule alerts to run unattended 24/7 and, should such an alert be triggered, send a message with critical data to your iPod Touch, smart phone, or any other mobile device.
FEATURES & BENEFITS
- Automatically send alerts to yourself, purchasing, suppliers, vendors, managers, etc.
- Create alerts to be triggered by data added to custom fields.
- Customize the alert message with your own text.
- Unlimited number of customizable alerts.
- No need to log into the system to receive alerts.
- Select to receive alert updates every 10 mins, hour, daily or only when a change occurs.
MOST POPULAR ALERTS
- Inventory shortages
- Overdue POs
- PO approvals
- Missing inventory for upcoming production
- Automatic vendor/customer follow-up
- ... and many more.
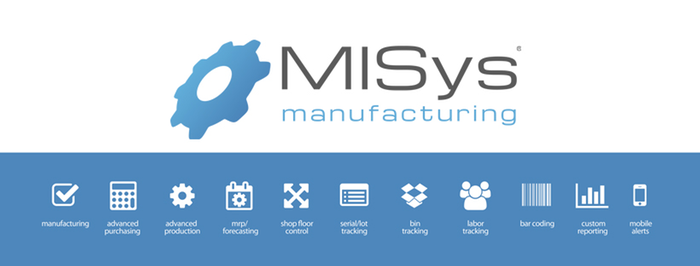
MISys EXT | Mobile App
Freedom. Flexibility. Speed. Use MISys EXT on any PC, tablet, smartphone or web-enabled device to process real-time MISys transactions using a web-based interface.
MISys Manufacturing EXT Functionality
- Log In/Out as a standard MISys Manufacturing company database User.
- Process any Stock Transfers, including Item Transfers, Assembly Transfers, Supplier Transfers, Component Transfers and Dispensing Tools.
- Process PO Receipts or Returns.
- Work Order processing, including Reserving, Allocating and Completing any Released Work Order.
- Manufacturing Order processing, including Starting, Starting/Scrapping individual components, and Completing any Released Manufacturing Order.
- Full Shop Operations processing, including Starting and Completing Operations, processing Time and Direct Labor transactions, and processing Scraps.
- Unique to MISys EXT, you can manage multiple active Operation Timers as part of Shop Operations processing.
- Create new Physical Inventory batches or to add new Detail lines to Physical Inventory batches.
- Print new Barcode labels.
- Any field may be populated by using the provided Finder, by scanning a barcode or by entering a quantity.
- Full integration with the Shop Floor Control, Serial/Lot Tracking and Bin Tracking modules.
- Transfer quantities of Items to Sales, or vice versa, as well as Sales Transfers as part of Work Order or Manufacturing order processing. Currently available for QuickBooks Online and Desktop, Sage 50 US, Sage 50 CA, Sage Intacct and Sage 300 ERP.
- Print labels using mobile and stationary Zebra Link-OS printers.
- Compatible with bluetooth scanning devices to populate fields in MISys EXT.
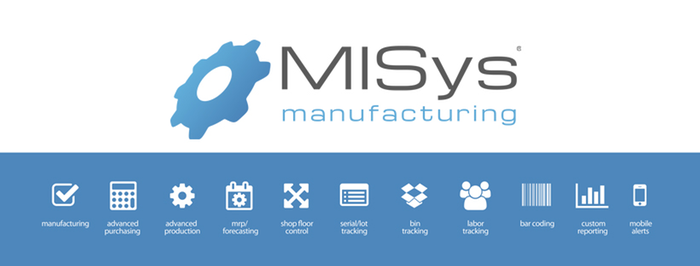